How do you electrify a freight train that is up to 50,000 times heavier and 50 times more powerful than a Tesla car? Can you just scale up existing electric car battery technology? Unfortunately, no, but we are on our way to solving this.
Electric vehicles (EVs) in the form of scooters and cars are becoming commonplace, but due to the size and weight, electrifying a locomotive fleet presents additional challenges.
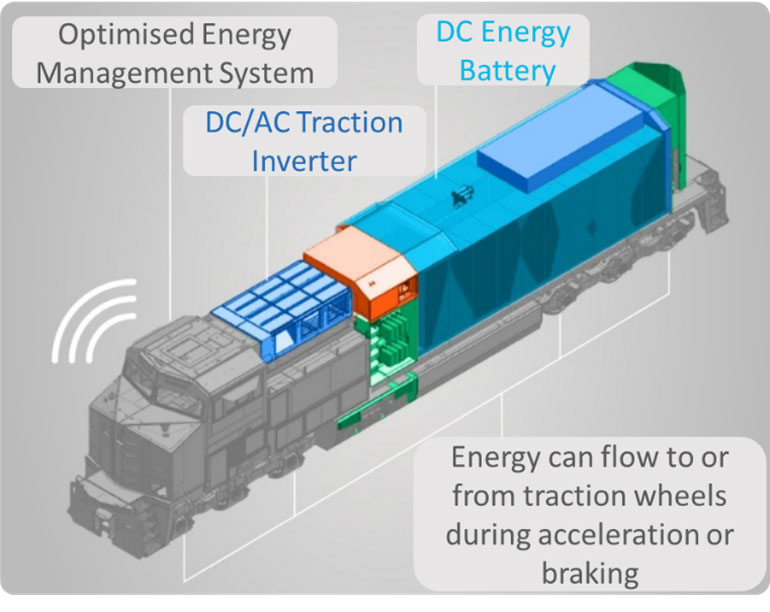
At present, more than 90 percent of railway freight (heavy haul) emissions are caused by the consumption of diesel. Therefore, locomotive companies around the world are looking to decarbonise their railway fleets by going electric. Conventionally, locomotive electrification is achieved by building overhead lines to connect electricity and electric motors.
However, this isn’t feasible in many rural areas, due to the capital cost. Battery-electric locomotives are an alternative and several demonstration units have already been tested globally (Figure 1). With the aim of decarbonising Australia’s railway fleet, a significant research project is underway involving the University of Queensland and rail company Aurizon, which moves ~250 million tonnes of freight in Australia each year.
They are seeking to answer these key questions:
What are the energy and power requirements of battery-electric locomotives?

Freight trains can weigh up to 100,000 tonnes (see BHP’s longest train in the world in Western Australia’s Pilbara region) and need to travel considerable distances along their routes (referred to as corridors). These transport giants therefore require a significant amount of energy to complete their routes. Even a lighter, shorter haul route can cover hundreds of kilometres – for example, the North Goonyella to Abbot Point route in Queensland (Newlands Corridor) is 232 km long. This shorter route would still require around 8.1 MWh of energy one way, around 80 times the energy stored in a Tesla S (assuming 100 kWh).
However, as with EVs, locomotive batteries can capture braking energy – which can dramatically reduce the size of the required battery pack. In diesel locomotives, the traction energy to drive the locomotive wheels originates from electricity generated by the onboard diesel engine. When the train needs to slow down or is travelling downhill (particularly when it is fully loaded), the dynamic braking system is applied, which generates electricity that is dissipated as heat and therefore lost.
However, in a battery-electric locomotive, this electricity can be captured and stored using the battery. These energy gains are dependent on the corridor terrain and driving conditions but can be estimated from braking data recorded for each corridor. Factoring this gained traction energy into the battery design can make the battery system more manageable. Returning to the Newlands Corridor example, traction energy would be able to provide approximately half (ca. 3.4 MWh) of the energy for the trip, reducing the required battery size to ca. 4.7 MWh. As such, regenerative braking can have a profound benefit in locomotive battery sizing.
How big is a loco battery?
Unlike the traditional lead-acid car battery, a lithium-ion battery pack in an EV is made up of many small cells. These cells can come in different formats – a cylindrical cell (similar to an AA battery), a prismatic cell (a flat, rectangular cell with a hard case) and a pouch cell (similar to a prismatic cell, but with a soft outer casing). When assessing the feasibility of vehicle electrification, a good starting point is to consider the cell energy density – the amount of energy per weight (Wh/kg) or volume (Wh/l) the cell contains.
However, in addition to this cell-level energy density, the different cell formats each have different packing and cooling efficiencies. This then can impact the size and weight (hence energy density) of the final battery pack. For example, an EV battery pack using cylindrical cells that have an energy density of around 250 Wh/kg would actually have an overall energy density of around 160 Wh/kg once the cells were incorporated into the battery pack – accounting for a 30 % reduction in energy density.
To meet the 4.7 MWh of energy we require for the Newlands Corridor example using cylindrical cells with an energy density of 250 Wh/kg, we would need around 19 tonnes (or around 8.5 m3) of cells. However, if calculated using the overall battery pack energy density, this increases the weight to around 29 tonnes (or around 21.5 m3). This is considerably heavier than the diesel fuel in the locomotive, which for a similar energy requirement would be 1.8 tonnes (or around 2 m3) of diesel.
But this doesn’t account for the large diesel engine that is required for a diesel-electric locomotive. The engine and associated ancillaries adds around 31 tonnes (or 25 m3) to the locomotive that is not required in a battery system. As such, replacing the diesel engine with a battery is feasible based on weight or size.
How cool is a battery?
Lithium-ion batteries have an optimal operating temperature. Operating too cold will reduce the amount of energy the battery can deliver, but running the battery at high temperatures can shorten the battery life and in extreme conditions can cause battery fires. Batteries also heat up during discharging or charging, and rapid charging and discharging can exacerbate this. It is therefore very important to keep batteries running at optimal temperatures (around 25 °C). During summer time, the average maximum temperatures in many parts of Australia are well above this temperature.
For example, in the Newlands Corridor in Queensland, the average maximum summer temperature is 34°C, but daily fluctuations can push the temperature closer to 40°C. To keep locomotive batteries at an optimal temperature, an active battery cooling system is critical in Australia.
This cooling becomes increasingly complex for large battery packs. The central cells are likely to be hotter than the cells on the outer side of the pack, which can cause rapid degradation of the central cells. The cooling systems add considerable weight and volume to the final battery pack. If assuming a proportionately scaled packing system from an EV, this accounts for an additional 10 tonnes of mass – a non-trivial additional weight.
These large and complex battery cooling systems can cost the system around 10-20 % of the energy on hot days in Australia. To avoid rapid degradation or potential fires, bespoke battery pack design will be required to accommodate the hot Australian conditions and allow for the most efficient cooling of these substantial battery systems.
But what is under the hood of that battery cell?
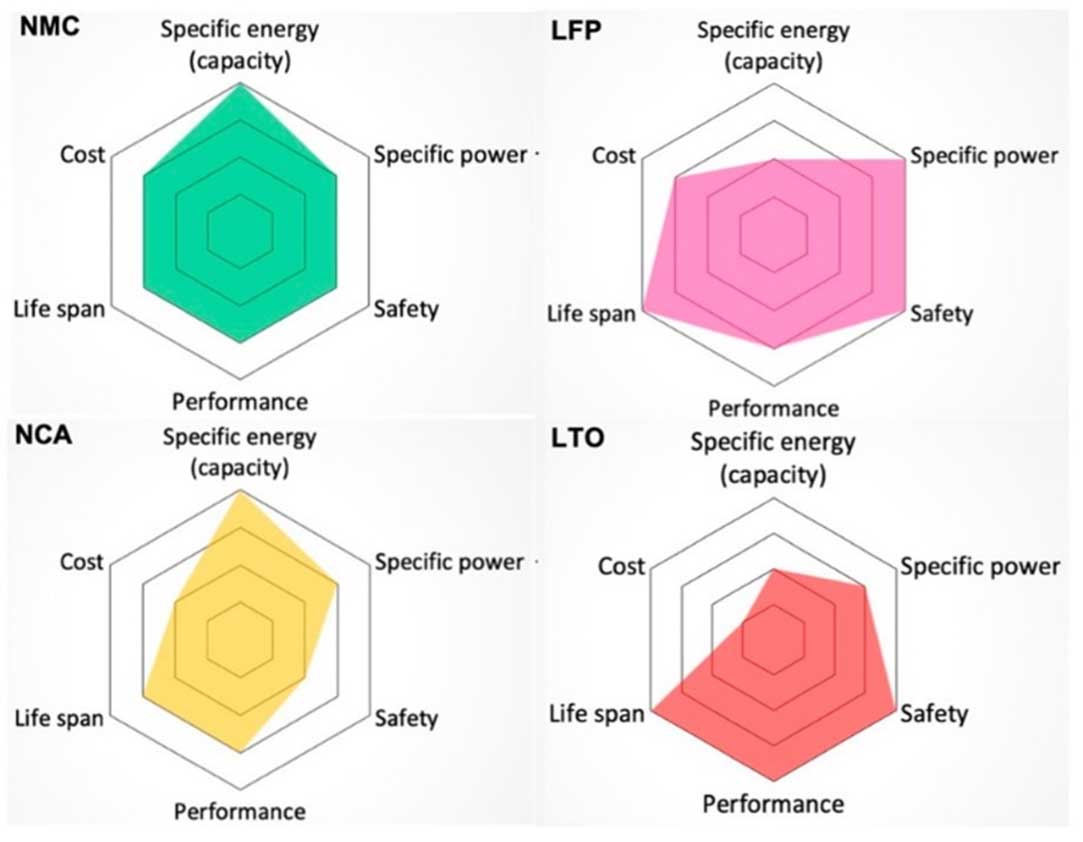
Each battery cell manufacturer has their own unique battery chemistry which balances important design metrics including energy density, specific power, safety, durability, and cost.
However, cells are often broadly grouped based on their generic cathode chemistry. Many car manufacturers use battery cells with a NMC (LiNiCoMnO2) chemistry. Tesla developed their own unique chemistry known as NCA (LiNiCoAlO2). For improved safety and a longer life, cell manufacturers are looking into LFP (LiFePO4) or LTO (Li4Ti5O12).
NMC and NCA possess relatively high energy density, which is beneficial for long-distance travel. LFP has a lower energy density, but has a great high-power performance and a better durability than NMC and NCA. The durability of the LTO is even higher than LFP, but LTO is expensive and the energy density is very low. This could mean the ultimate train battery is a synergistic combination of high-energy materials (NMC or NCA) and high-power materials (LFP or LTO). The NMC/NCA could be used for slow discharge over the entire trip and the high power and durable LFP or LTO could be used to store and release energy quickly – during acceleration and braking.
Safety is of critical importance when designing any battery system. Cells can be unsafe due to inherent instability of the materials, but also due to defects in the manufacturing processes or inadequate battery management system (which manages the current, voltage, and temperature the battery pack operates under). LFP has a high thermal stability – making it inherently safer than both NMC and NCA. However, the less stable chemistries, such as NMC and NCA, can be made safe through cell material engineering and excellent control of the cell operating conditions.
What is the future of battery technology?
Battery technology has evolved enormously in the past few decades from Ni-Cd (less than 100 Wh/kg) to present-day graphite-NCA (near 300 Wh/kg) (Figure 4). However, for mobility electrification, manufacturers are looking for even higher energy densities – which will increase driving distance and/or reduce the battery size. Rapid battery technology improvements are continuously increasing energy density, improving durability, and looking at reducing production costs.
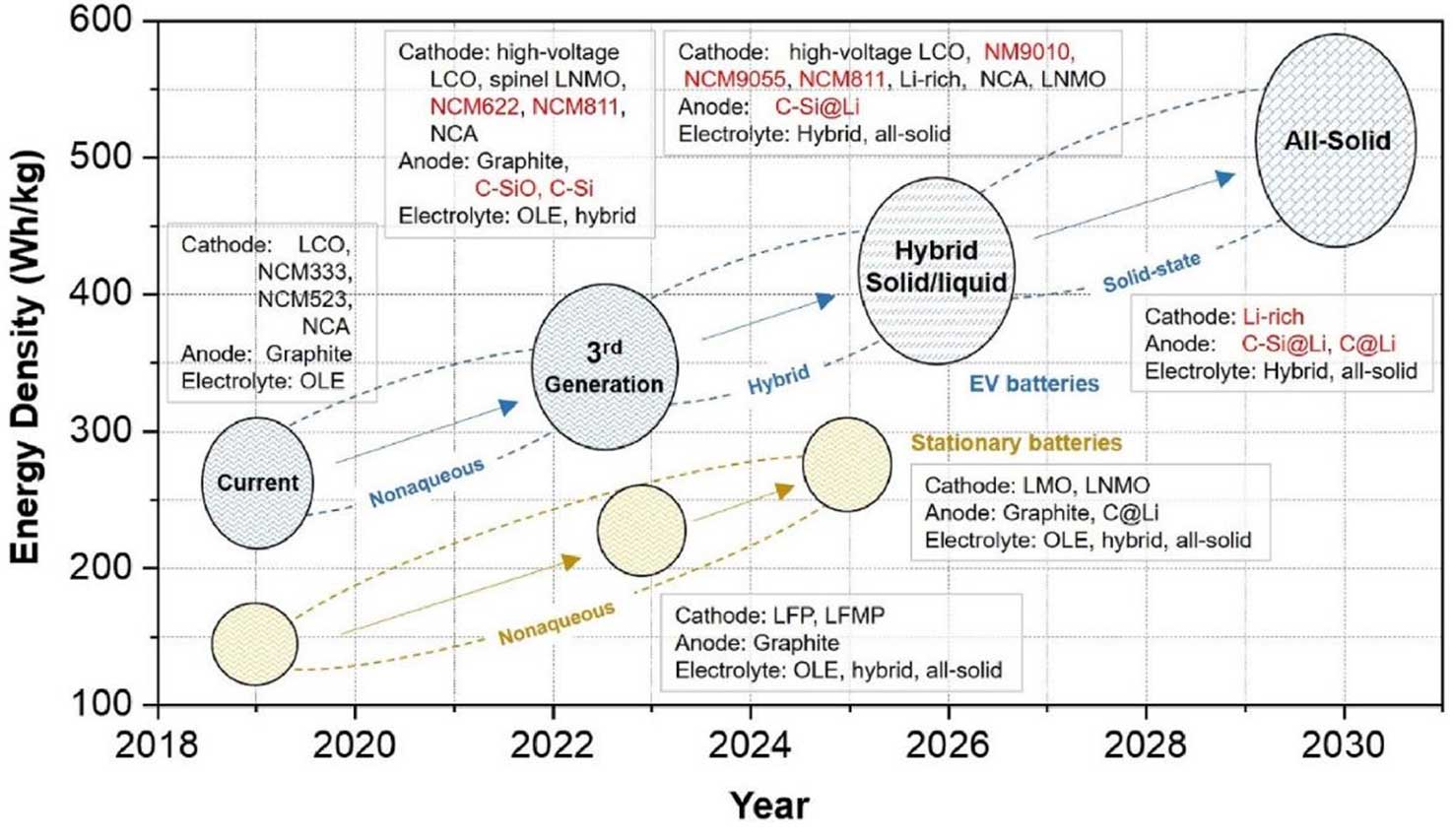
There are several new battery chemistries that are forecast to be the batteries of the future. This includes solid-state batteries (SSBs), which can achieve a cell energy density of up to around 500 Wh/kg when using Li metal as anode (Figure 4). SSBs use a solid-state electrolyte, which makes them safer as the flammable liquid electrolyte is removed.
The excellent thermal safety can also simplify the cooling system (reducing both space and weight of the final pack) and permits for faster charging/discharging. Therefore, the SSBs have a twofold benefit: high energy density and improved fast charging/discharging. There are many start-ups and automakers looking to propel SSB technology forward. However, besides several material engineering problems, new production lines need to be redesigned to suit SSBs mass production.
In Summary
To decarbonise Australian railway fleets with batteries, switching from diesel-electric locomotives to battery-electric locomotives is a promising solution. Although battery-electric locomotives benefit from the rapid battery development of the automotive industry, it is important to recognise that heavy haul rail presents additional challenges due to the scale of the battery system needed. But don’t be surprised when you see a battery-electric freight train pass you in the coming years.
Authors
UQ: Dr Ruth Knibbe and Professor Paul Meehan
Aurizon: Damien Harding and Roger Buckley